顯著提升充電效率,基本半導體應用于高壓快充的E2B碳化硅功率模塊方案解析
發表時間:2024-07-03 19:05
摘 要
充電樁采用碳化硅模塊可以增加30﹪的輸出功率,減少50﹪的損耗。目前在充電樁領域,碳化硅應用處于快速增長階段,預計到2025年將提升至35﹪,市場規模將達200億元。
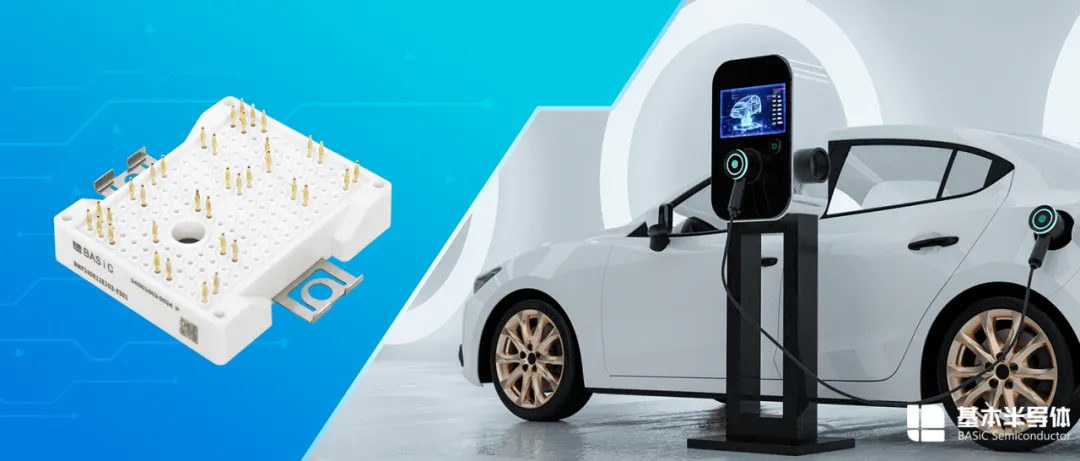
年來,充電時長已經成為影響新能源汽車駕駛體驗的關鍵因素,市場對提高車輛充電速度的需求變得越來越迫切。高電壓和大電流都可縮短充電時間,但考慮到銅線損耗的因素,高壓大功率比大電流方案更有效率。而要提升充電速度,必然要關注大功率充電,在不提高整車電壓平臺的條件下,必須增大充電電流,但這樣也會導致端子、線纜的發熱量增加,繼而溫度升高。持續高溫容易損害充電裝置,嚴重的還會引發安全事故,為避免這種情況,必須將充電槍端子及線纜的發熱量及溫升降低,常用的方法就是增大導體截面積。然而增大導體截面積后會增加線纜的重量,用戶使用會很不方便。考慮到充電槍的電流約束,適合的辦法是通過提升電壓平臺實現大功率充電。
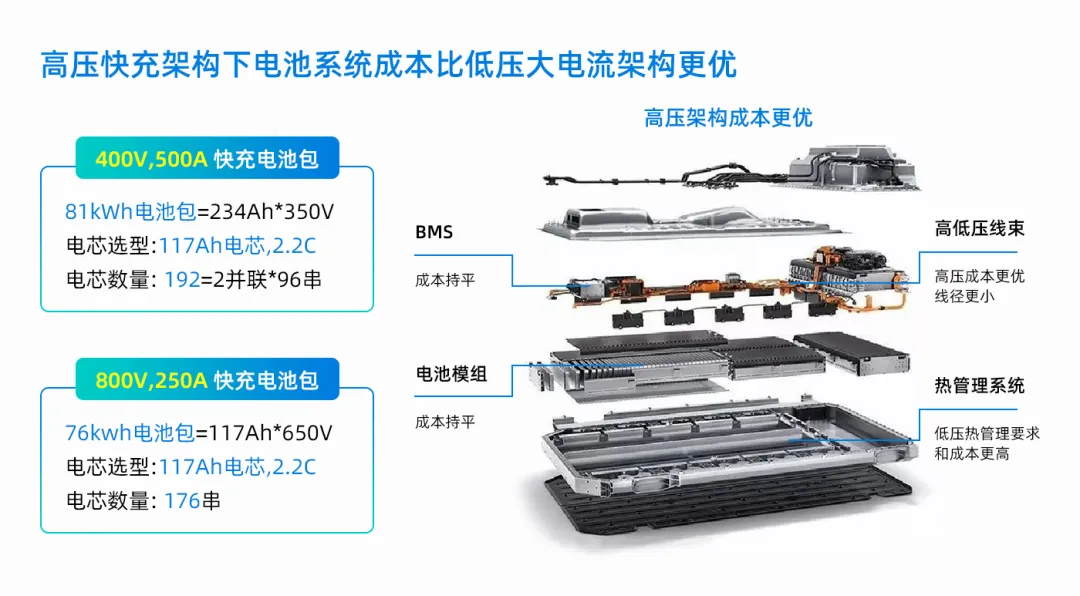
圖1 高壓快充架構下電池系統成本與低壓大電流架構的對比
目前主流車企均在布局高壓快充車型,預計2026年800伏以上高壓車型銷量將過半,但我國適配高壓快充的高壓充電樁數量不足。為此,主流車企和充電運營商正加快研發推出大功率快充樁,亟需更耐高壓、耐高溫、更小型化的新型功率器件,以滿足充電設備對效率和安全的更高要求。
作為第三代半導體材料,碳化硅具有寬禁帶、高熱導率、高擊穿場強、高飽和電子漂移速率等優異特性。與傳統硅材料比較,碳化硅器件能有效滿足充電樁設備耐高壓、耐高溫、更小型化新型器件的需求,幫助實現新能源汽車快速充電的目標。此外,碳化硅還能提高單位功率密度,減小模塊體積并簡化電路設計,對降低充電樁成本起到重要作用。
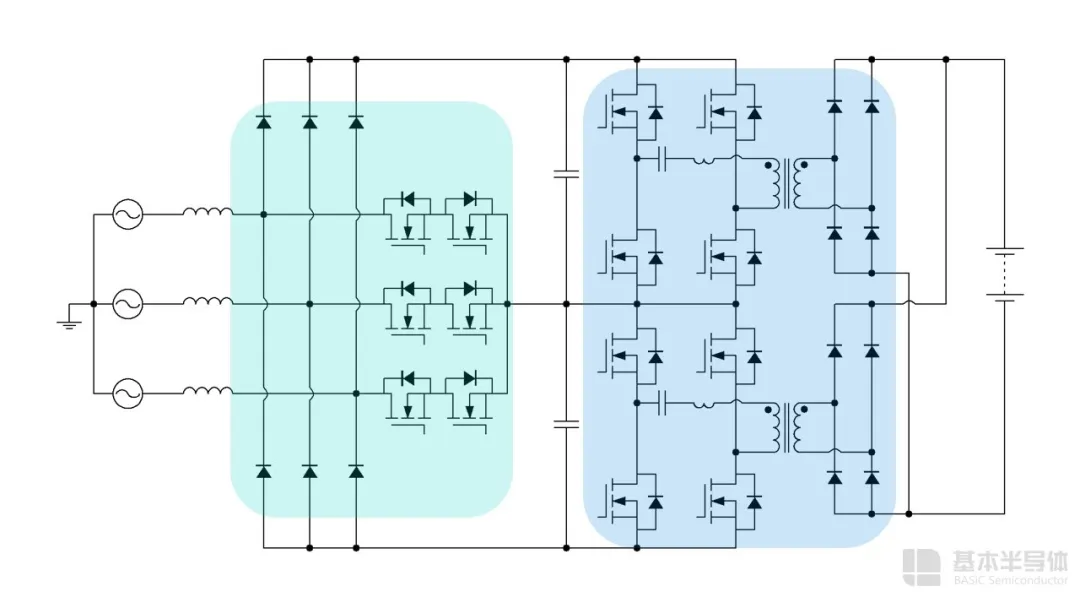
圖2 傳統硅功率器件單向充電樁方案
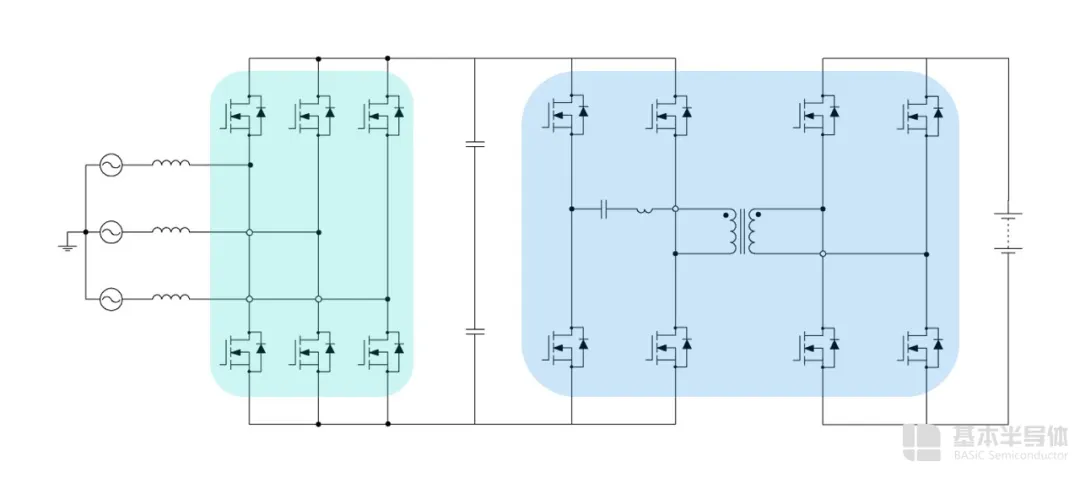
圖3 碳化硅功率器件雙向充電樁方案
傳統硅方案充電樁模塊電源中,DC/DC拓撲采用650V硅基超結MOSFET組成兩個全橋串聯的LLC,使用1200V碳化硅MOSFET以后,系統可以簡化為一個LLC諧振回路,器件數量大幅度減少,有利于提升系統可靠性。尤其是關斷損耗更小的碳化硅MOSFET,更適合充電樁電源模塊DC/DC部分的LLC/移相全橋等電路拓撲。
同時,1200V/40mΩ碳化硅MOSFET分立器件在風光儲充、車載充電、汽車空調等領域的電源模塊上被廣泛應用,規模優勢使碳化硅MOSFET成本進一步降低,使得用1200V碳化硅MOSFET的系統成本比使用650V硅基超結MOSFET的更低,產品更具有競爭力。
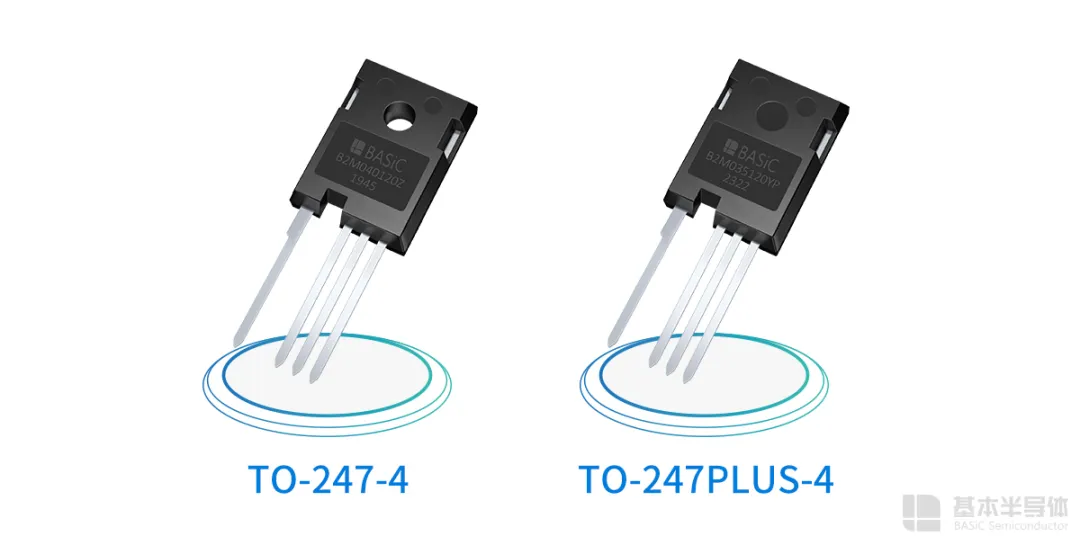
圖4 基本半導體1200V碳化硅MOSFET
此外,大功率(50kW~60kW)的充電模塊功率密度高,體積有限,如果采用分立器件,并聯數量會很多,給均流、安裝和散熱帶來了非常高的挑戰,而采用碳化硅 MOSFET模塊方案,則可以很好地解決上述問題。
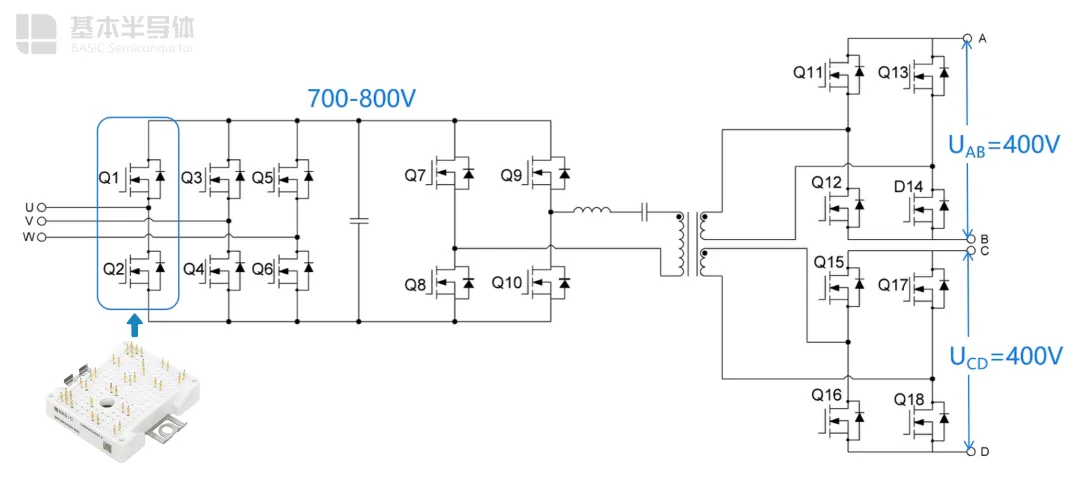
圖5 基本半導體1200V碳化硅MOSFET E2B半橋模塊在充電樁中的應用
基本半導體PcoreTM2 E2B 全碳化硅半橋MOSFET模塊BMF240R120E2G3基于高性能晶圓平臺設計,在比導通電阻、開關損耗、抗誤導通、可靠性等方面表現出色。高溫(Tvj=150℃)下的RDS(on)參數僅比常溫(Tvj=25℃)時增加1.4倍左右。產品內置碳化硅肖特基二極管,使得續流二極管基本沒有反向恢復行為,大幅降低模塊的開通損耗。產品還引入氮化硅(Si3N4)AMB陶瓷基板及高溫焊料,可改善長期高溫度沖擊循環的CTE失配,陶瓷板的可靠性大幅提升。
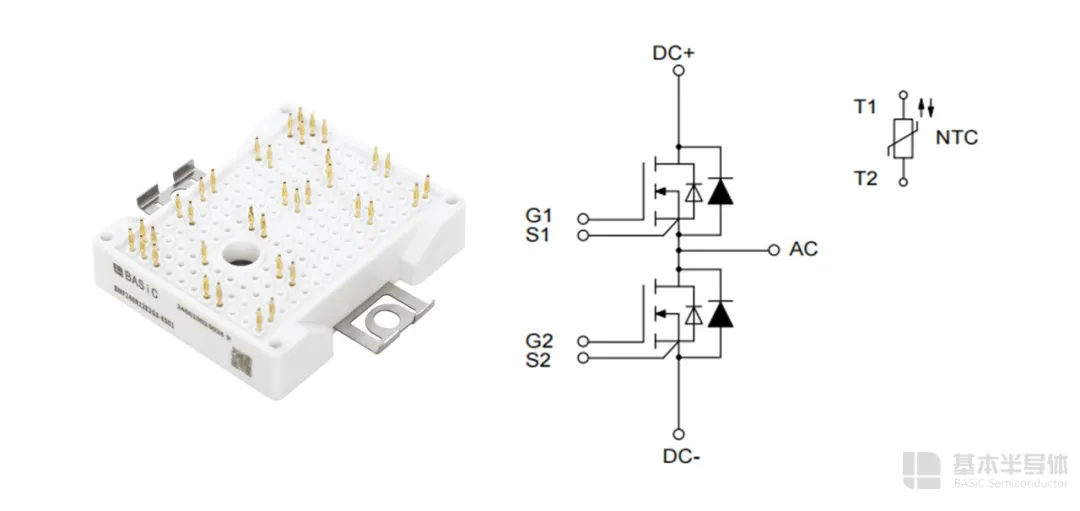
圖6 PcoreTM2 E2B 全碳化硅半橋MOSFET模塊BMF240R120E2G3
在高壓快充的大背景下,以基本半導體為代表的碳化硅功率器件企業將不斷加大研發力度,確保技術能緊跟行業趨勢和市場需求,為充電樁設備制造企業提供更高性能的碳化硅功率器件。隨著新能源汽車、光伏產業的快速發展,碳化硅器件在電力設備行業中還將有更廣泛的應用,其市場規模還有的成長空間,預計碳化硅功率器件在光伏逆變器的滲透率將從 2020年的10﹪增長至 2048年的85﹪。
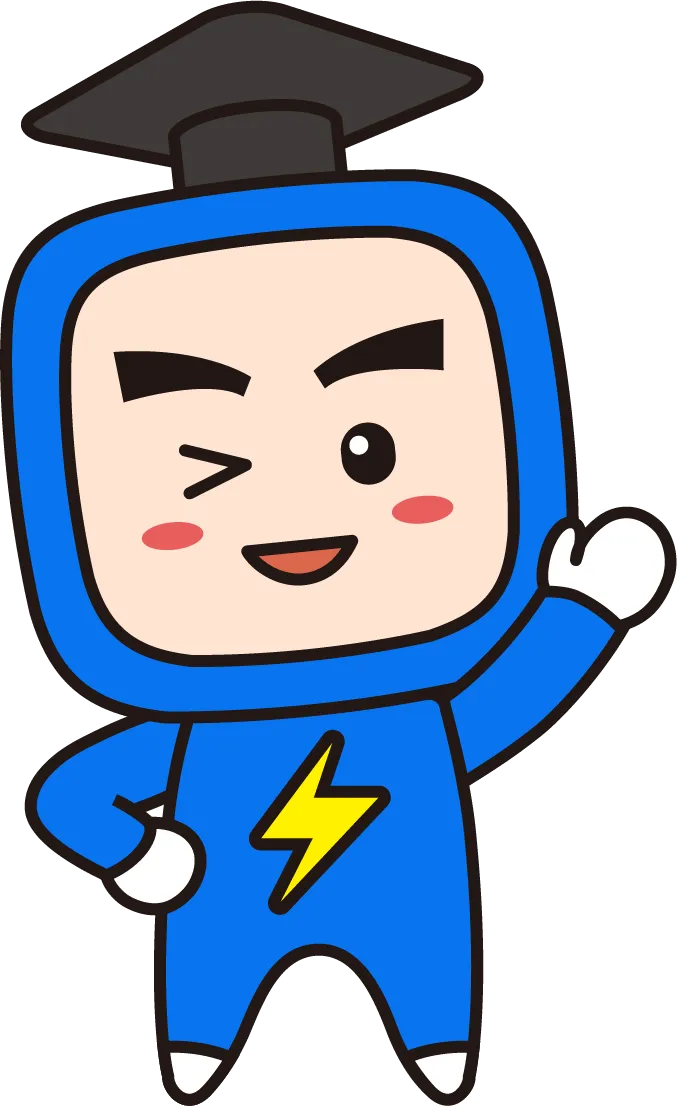